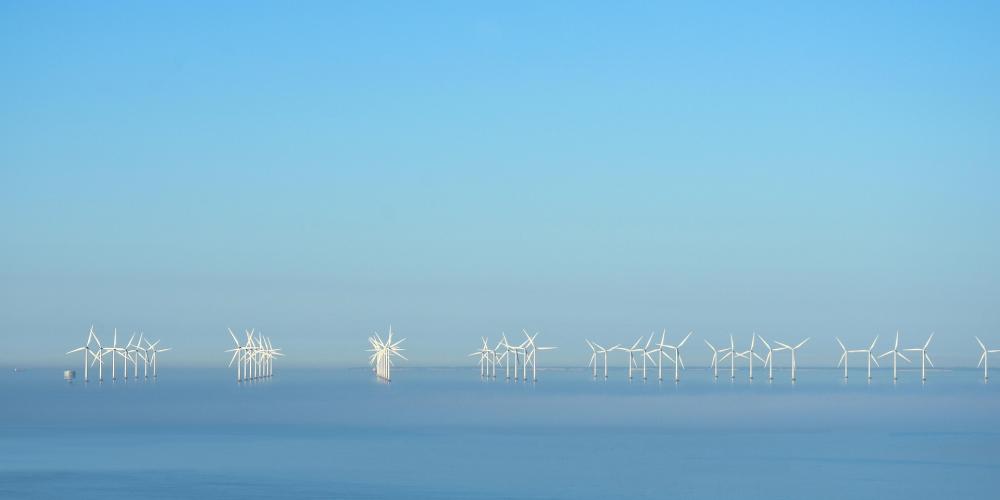
A researcher from the VUB has developed a system that makes it possible to predict the failure of wind turbines due to early failure of components. He has specialized in condition monitoring, which involves monitoring the state of the machine using data generated by the sensors on the wind turbine, along with artificial intelligence. "If operators can anticipate that a particular component will fail, they can replace it during regular maintenance, so the turbine doesn't have to be idle," says Dr. Xavier Chesterman, who completed his PhD on this complex issue.
Early failure of turbine components, which results in downtime of the wind turbine, has an impact on profitability. On average, an offshore wind turbine fails 8.3 times per year (Carroll et al., 2016). Some components, depending on the type of wind turbine, are more prone to defects. These often involve the generator, the gearbox, or subcomponents of these parts, such as bearings and other moving elements.
The downtime costs operators, both offshore and on land, a lot of money. "Replacing those components during normal maintenance can significantly reduce maintenance costs and downtime," says Chesterman. "Predicting and diagnosing wind turbine failures is currently a problem that has not yet been adequately solved. A useful methodology must be able to detect various types of faults before they actually occur. The methodology must not only be able to detect when a component starts behaving abnormally but also interpret patterns in the abnormal behavior and prevent the defect from happening."
The sensors measure a wide range of things on a turbine, such as vibrations, abnormal temperature increases, and more. The main goal of the research was the development of an automatic fault prediction and diagnosis system for the drivetrain of wind turbines. For this, data that are standardly available, namely the so-called 10-minute Supervisory Control and Data Acquisition (SCADA) data and status logbook data, were used. Chesterman focused primarily on one type of signal: temperature. His system had to be capable of predicting failures and faults in the wind turbine drivetrain in advance by analyzing temperature signals from various components. "Furthermore, the system had to determine the type of fault based on patterns in the abnormal behavior of the wind turbine," Chesterman explains. "The system uses artificial intelligence (AI), more specifically machine learning and data mining. The vast amount of data makes it more difficult for experts to analyze and interpret patterns. Sometimes it's a combination of various signals that indicates where the failure will occur."
The developed system was practically tested on data from three operational wind turbine parks in the North Sea and the Baltic Sea. "The validation showed that the most effective fault prediction methodology can accurately and early detect certain faults, with an 80% confidence rate."
Chesterman now wants to take it a step further in his postdoc research. He plans to apply his data analysis techniques to other types of machines, such as compressors and agricultural machinery.