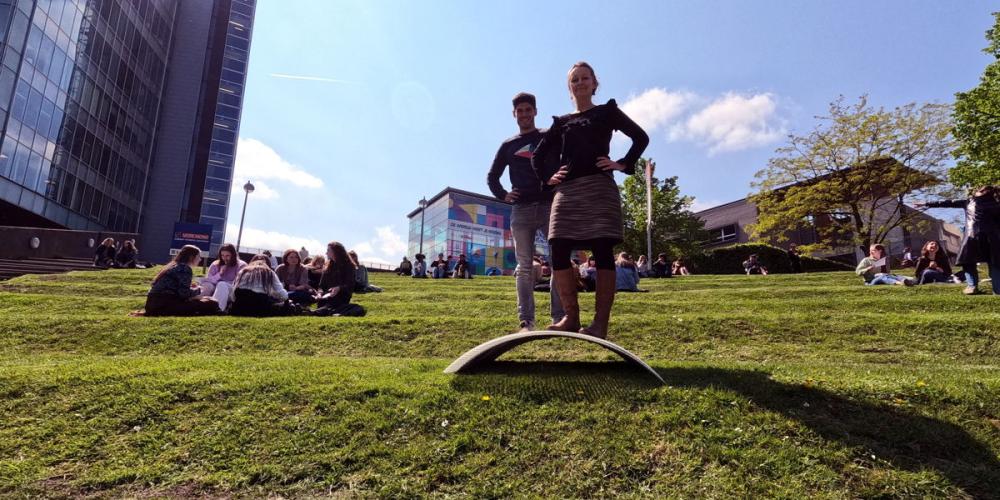
Researchers and engineers at the VUB research group Mechanics of Materials and Constructions (MeMC) are experimenting extensively with textile reinforced concrete. These are not ordinary textiles that clothes are made from, but technical textiles, made of carbon, glass or basalt fibres. Using this kind of material for reinforcement can reduce the amount of concrete in a structure by up to 80%, representing a serious economic and environmental gain.
“But that’s not even the biggest advantage,” says postgraduate researcher and structural engineer Michael El Kadi of MeMC. “This is more about durability: textile-reinforced concrete doesn’t suffer from degradation because it no longer contains corroding materials. In traditional concrete with iron reinforcement, you need to provide a layer of concrete at least 3 to 5 cm thick around the reinforcement mesh, which allows the iron to be shielded from the air and can delay corrosion. This is also why concrete is always poured so thickly. With textile reinforced concrete, you don’t need such a thick protective layer, so in some cases a concrete thickness of 2 to 3cm is sufficient for strength.”
All this means that spans can be realised with barely a fifth of the previously required amount of concrete. “All concrete is used on the structure in that case,” says El Kadi. “In addition, technical reinforcement textiles allow very flexible handling of shapes. We can easily cast thin curved concrete vaults with it, which are also very sturdy. In fact, the possible applications are virtually unlimited.”
According to the researchers, the results in terms of bearing capacity and strength of textile reinforced concrete are similar to those of traditional concrete. “That largely depends on the reinforcement chosen,” says El Kadi. “Glass textiles are less rigid than carbon textiles, which are actually sturdier than steel. Textile reinforcement also opens up prospects for precast applications. Bespoke concrete structures can be prepared in a workshop before they are transported to the construction site. By using textile reinforcement, those structural elements are also a lot lighter, allowing more elements to be lifted into place by hand.”
The only drawback is the price. Reinforcement textiles are relatively expensive – though this is partly offset by resource savings. “And there is an ecological gain to take into account,” says El Kadi. “Every kilogram of raw material that doesn’t have to be mined means profit.”
Finally, due to its low volume, textile reinforced concrete also lends itself well to finer restoration work. “You can use it relatively easily to repair cracks and fissures in buildings,” says El Kadi. That’s good news for companies involved in restoring the concrete buildings that have been built so widely over the past century, as they could now have a new lease of life for longer.